
圖4 單邊切口梁法測試斷裂韌性示意圖
2 高爐冶金礦渣特性研究
2.1 高爐渣的產生及預處理
在高爐冶煉生鐵的過程中會產生許多副產品,高爐渣作為被排除的一種廢渣,它是由礦石中的一些無法煉進生鐵中的雜質、灰分和助熔劑所形成的易熔物質。采用水淬?;に噷Ω郀t渣進行冷卻處理,90%以上的高爐渣被處理成粒狀水渣,其中玻璃質含量高達95%,具有良好的潛在活性。如圖5所示,在1 400~1 600 ℃的爐溫下,鐵礦石中的鋁礬土、脈石與助熔劑高溫下進行反應,生成易熔的鈣鋁酸鹽,其反應方程式如下:
CaCO3=CaO+CO2↑
(5)
3CaO+Al2O3=Ca3Al2O6
(6)
3CaO+SiO2=CaSiO3
(7)
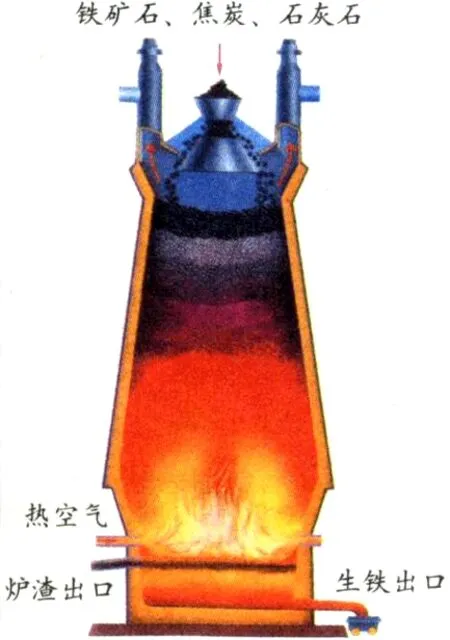
圖5 煉鐵高爐及爐內化學變化過程示意圖
由于未經處理的高爐冶金礦渣粒徑很大,使用前一般會對其進行一定預處理。高爐渣的活性與冶煉條件、冷卻條件以及鐵礦石和造渣原料的化學成分等密切相關。本文所研究的高爐渣產自河南某鋼鐵公司,其粒度分布見表3,高爐渣顆粒分布在0.1~5 mm之間,大多數顆粒粒徑為1~2 mm。為進一步探究高爐渣的特性,利用高能球磨機對高爐渣進行球磨處理,球磨30 min后將其置于干燥箱中至恒重,過200目篩后妥善放置以備使用。圖6是高爐渣原料和球磨處理30 min后高爐渣的微觀形貌,由圖可知,高爐渣為灰白色,粒度為2~10 μm。

表3 篩分法測得的高爐渣粒度分布
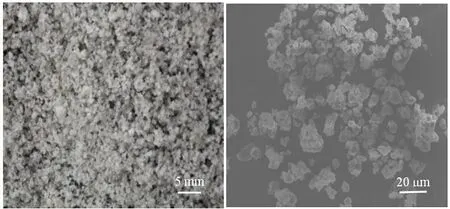
圖6 高爐渣原料和球磨處理高爐渣的SEM圖
2.2 化學組成及物相組成
高爐渣的化學組成因產地不同而存在差異,取決于礦石質量、助熔劑成分、焦炭量以及冶煉生鐵的種類,大體上含有Al2O3、SiO2、CaO等化合物。通過XRF分析,高爐渣的化學組成如表4所示,主要為CaO、SiO2、Al2O3、MgO等硅酸鹽成分,并含有少量的Fe2O3、TiO2和ZrO2等晶核劑。

表4 高爐渣的化學組成 /%
通過XRD分析高爐渣粉體的物相組成如圖7所示。從圖中可以看出,在25°~40°范圍存在非晶態“饅頭峰”,表明高爐渣為無定形玻璃態。
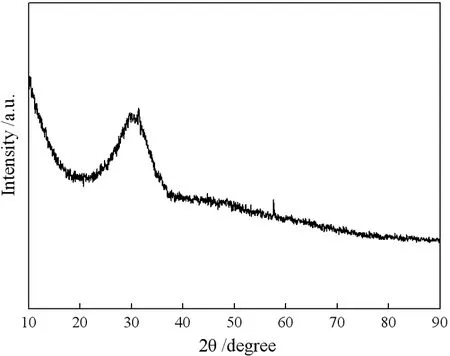
圖7 高爐渣的XRD圖譜
2.3 差熱分析及析晶特性
高爐渣差熱分析結果如圖8所示。從圖中775 ℃處的吸熱峰可知,玻璃體中的晶核劑(TiO2、Fe2O3)在775 ℃吸熱形核;無定形玻璃態的高爐渣在812~ 855 ℃發生析晶,整個析晶過程伴隨熱量放出,形成放熱峰。
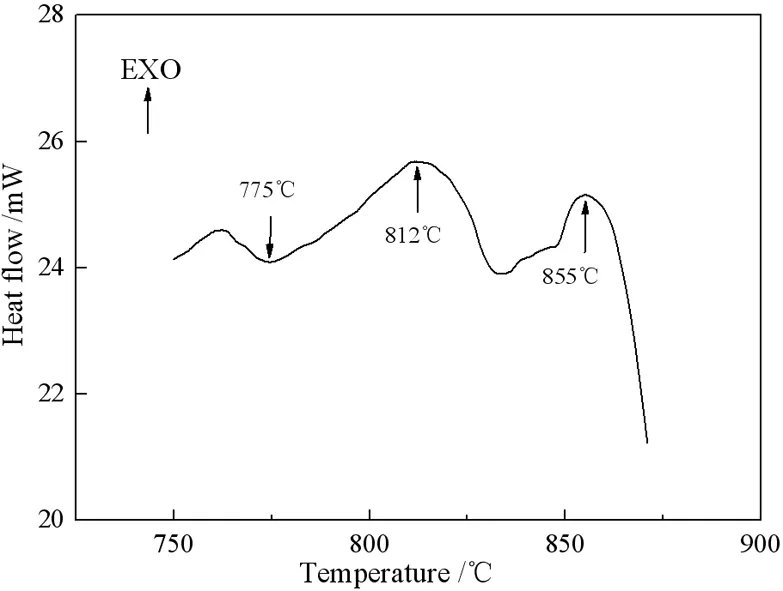
圖8 高爐渣的DSC曲線
將球磨粉碎后的高爐渣壓片成型,在馬弗爐中855 ℃熱處理1 h,對高爐渣進行析晶處理,圖9為高爐渣在855 ℃保溫1 h晶化處理后的XRD曲線,從圖中可以看出,晶化處理后高爐渣的主晶相是以Ca2Al2SiO7為基礎的固溶體,在掃描電鏡下的微觀形貌中可觀察到1 μm左右的微晶(如圖10所示)。
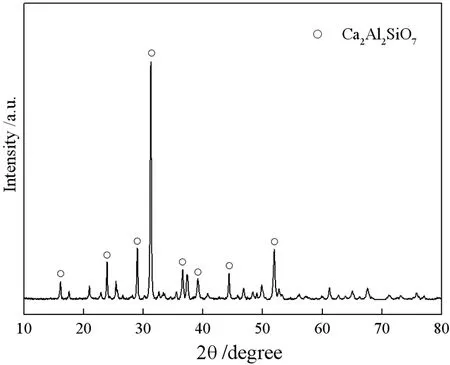
圖9 熱處理后高爐渣的XRD圖譜
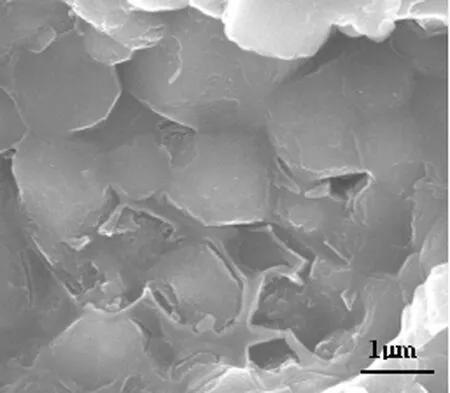
圖10 晶化處理后高爐渣的SEM圖
圖11為高爐渣析晶過程的示意圖。從圖(a)可以看出,室溫下高爐渣顆粒間存在一定空隙;在溫度升高至核化溫度的過程中(圖b),玻璃顆粒逐漸軟化,黏度降低,玻璃相形成晶核并發生核化;當達到晶化溫度時(圖c),晶粒長大并逐漸形成玻璃晶界;圖(d)為燒結過程結束,在玻璃體中形成的晶粒均勻分布的微晶玻璃。
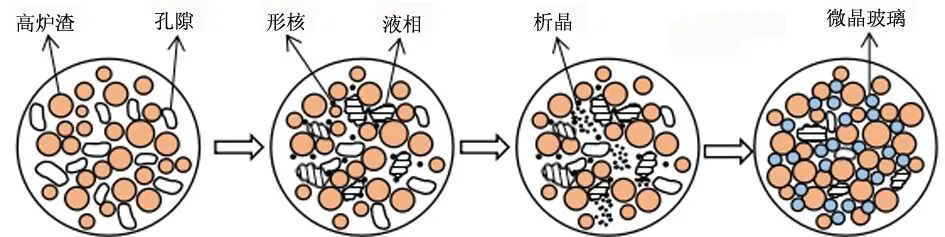
圖11 高爐渣析晶過程示意圖
3 結果與討論
3.1 以納米TiC為增強相制備ZTA陶瓷
圖12為Al2O3(含15%納米Al2O3)和ZrO2的質量比為73,分別添加0%、2%、4%、6%和8%(均為質量分數,下同)的納米TiC,1 650 ℃下燒結30 min,所得樣品相對密度與顯氣孔率隨TiC含量的變化。由圖可知,TiC含量為0~6%時,材料的相對密度在99%以上,當TiC含量為8%時,相對密度開始降低;材料的顯氣孔率在TiC含量為6%時出現最大值,為0.4%。這是由于納米TiC的含量較少時,與納米ZrO2均勻地分散到基體中以填充孔隙,而且納米Al2O3顆粒具有較大的表面能也將促進燒結,使得復合陶瓷致密化程度高、孔隙率低。隨著納米TiC含量逐漸升高,由于其具有較大的表面活性而難以分散,易發生團聚,使納米顆粒失去了原有的納米尺寸效應,影響了坯體的密度,且在燒結過程中團聚體中產生的氣體難以排出,形成閉氣孔,影響ZTA陶瓷的致密化。

圖12 TiC含量對ZTA陶瓷相對密度和顯氣孔率的影響
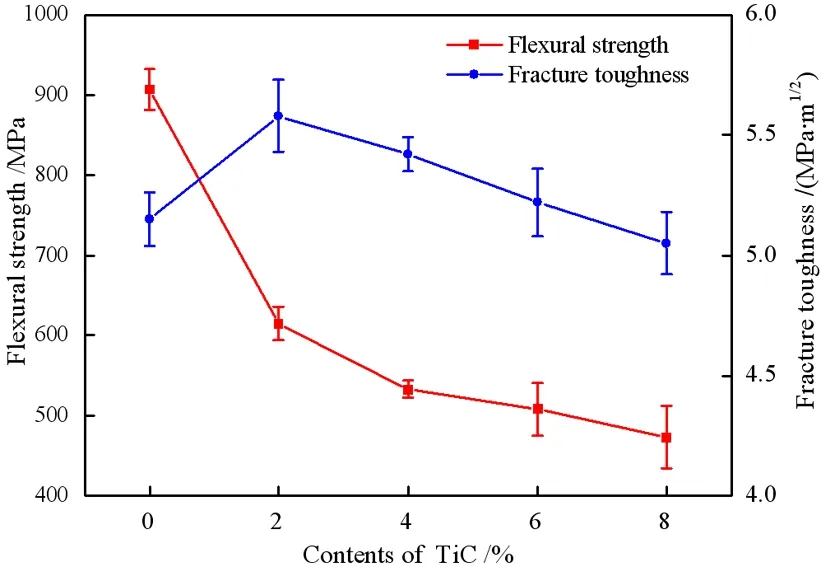
圖13 TiC含量對ZTA陶瓷抗彎強度和斷裂韌性的影響
圖13是在1 650 ℃燒結30 min時ZTA陶瓷的抗彎強度和斷裂韌性隨納米TiC含量的變化。從圖中可以看出,隨著納米TiC含量的增加,復合陶瓷的抗彎強度逐漸減小,當TiC含量為2%時,抗彎強度為615 MPa;由圖可知,隨著納米TiC含量的逐漸增加,陶瓷的斷裂韌性逐漸降低,未添加納米TiC樣品的斷裂韌性為5.15 MPa·m1/2,納米TiC含量為2%時,斷裂韌性明顯提高,可達5.58 MPa·m1/2。
圖14為不同TiC含量的ZTA陶瓷經1 650 ℃燒結后斷面的微觀形貌。從圖(a)中可以看出,向ZTA體系中添加2%的納米TiC,晶粒大小均勻,組織結構致密,陶瓷的斷裂方式為沿晶斷裂和穿晶斷裂同時存在。由于在燒結過程中,在燒結驅動力的作用下,細小的納米Al2O3、ZrO2和TiC顆粒充填在基體的孔隙中,孔隙率降低,晶粒間結合更為緊密。如圖(b)所示,當TiC含量增加到4%時,納米顆粒已經開始出現團聚的現象,團聚體與Al2O3之間存在空隙,這是由于TiC和ZrO2顆粒細小,具有較大表面能,在高溫下極易燒結成大粒徑的團聚體,納米TiC和ZrO2團聚的大顆粒和Al2O3晶粒之間會形成一定的晶界阻隔,在Al2O3基體內形成大量的微裂紋和氣孔缺陷。如圖(c)所示,當納米TiC含量為6%時,由于納米TiC和ZrO2顆粒填充Al2O3基體空隙效果明顯,復合陶瓷的相對密度逐漸增加;然而在納米TiC含量為8%時,納米TiC含量達到臨界值,填充效果減弱,過多的納米顆粒形成團聚影響陶瓷致密,造成相對密度降低。從圖(d)中還可以看出大顆粒的Al2O3堆垛,基體中形成大量的缺陷和燒結過程中未及時排出的氣體形成的閉氣孔,影響了ZTA陶瓷的力學性能,上述結果分析和復合陶瓷的物理性能與力學性能數據相符。
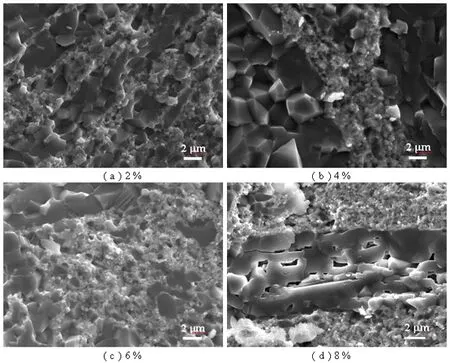
圖14 不同TiC含量的ZTA陶瓷斷面SEM圖
添加納米TiC粉體能顯著改善ZTA陶瓷的力學性能,由于納米TiC顆粒能抑制Al2O3、ZrO2晶粒生長,使組織結構均勻穩定且致密,極大程度降低基體的閉氣孔和缺陷數量,此外,硬質相對晶界的釘扎作用,以及陶瓷內部晶粒的細化,使基體中產生大量的微裂紋和次晶界,增加晶界體積比,并增強晶界結合強度,致使裂紋擴展過程中沿晶內擴展形成穿晶斷裂,有利于提高復合陶瓷的常溫和高溫力學性能。
3.2 高爐冶金礦渣對ZTA陶瓷性能的影響
通過對高爐冶金礦渣的特性分析可知,由于在形成過程中的急速降溫,造成其為一種玻璃態物質,具有較高的能態,并含有大量的陶瓷傳統燒結助劑成分,如CaO、SiO2、Al2O3、MgO等。通過對其差熱分析及析晶特性研究可知,高爐渣原料經高溫煅燒,可得到大量的Ca2Al2SiO7晶相,Ca2Al2SiO7具有良好的物理性能和力學性能。因此,高爐冶金礦渣在ZTA陶瓷燒結過程中的作用,具有很大的研究意義。
為了研究高爐渣在ZTA陶瓷燒結中的作用,在上述配方的基礎上,設定高爐渣的添加量(質量分數,下同)為0%、2%、4%、6%、8%五個組分,各組配方原料的質量分數(見表5)。燒結溫度為1550 ℃,燒結時間為30 min,燒結壓力為30 MPa,燒結后通過水冷降溫至200 ℃,并隨爐冷卻到室溫。最后對ZTA陶瓷的物理性能、力學性能和顯微結構進行分析表征。
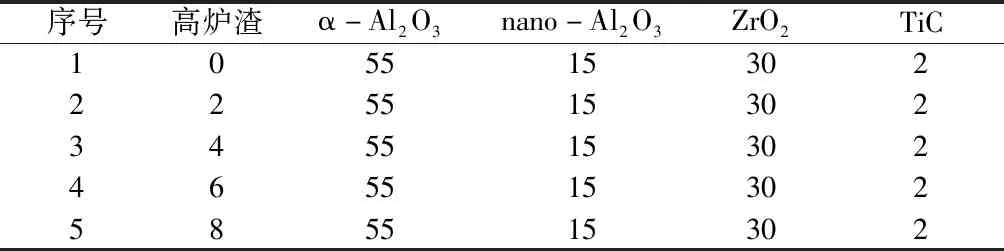
表5 各原料的質量分數 /%
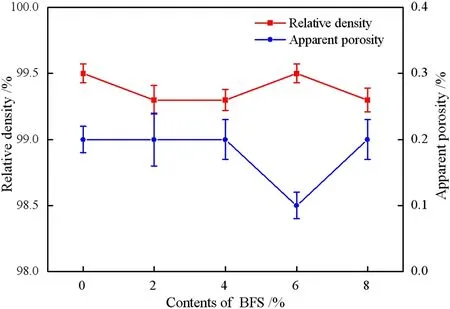
圖15 不同高爐渣添加量的ZTA陶瓷相對密度和顯氣孔率
圖15為高爐渣添加量對ZTA陶瓷相對密度和顯氣孔率的影響。從圖中可知,隨著高爐渣添加量的升高,ZTA陶瓷的相對密度在99.5%上下波動且變化不大;顯氣孔率先減小后增大,當高爐渣添加量為6%時,陶瓷的顯氣孔率低至0.1%,致密度達到99.5%。說明高爐渣起到了助熔作用,添加適量的高爐渣可以降低ZTA陶瓷的顯氣孔率。由于納米Al2O3和ZrO2均勻分布于基體的孔隙中,高溫燒結的微晶玻璃相,使原本充填性好的陶瓷基體更加致密,有利于ZTA陶瓷力學性能的提升。
不同高爐渣添加量的ZTA陶瓷經1 550 ℃燒結的抗彎強度和斷裂韌性變化曲線如圖16所示。從圖中可以看出,未添加高爐渣的ZTA陶瓷的抗彎強度和斷裂韌性分別為565 MPa和5.28 MPa·m1/2,當高爐渣添加量為4%,復合陶瓷的抗彎強度達到650 MPa,斷裂韌性達到6.03 MPa·m1/2,分別提高了15%和14.2%。
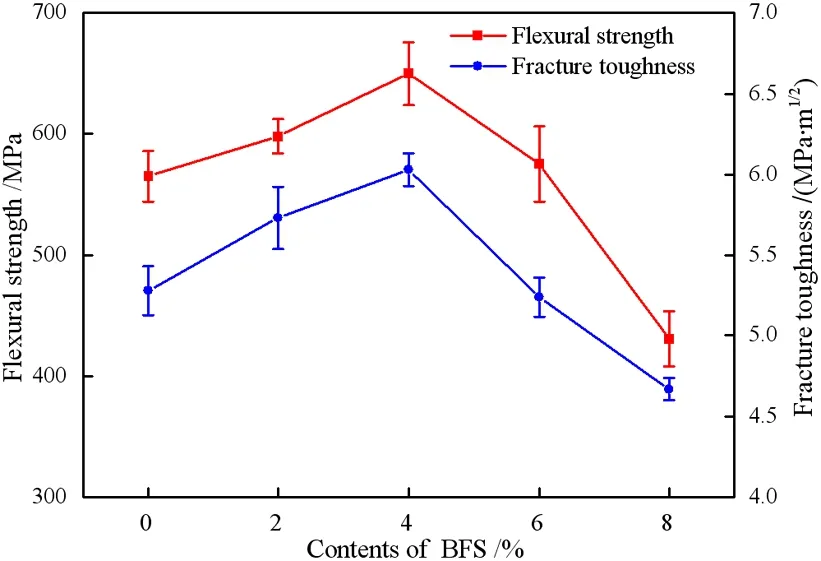
圖16 不同高爐渣添加量的ZTA陶瓷抗彎強度和斷裂韌性
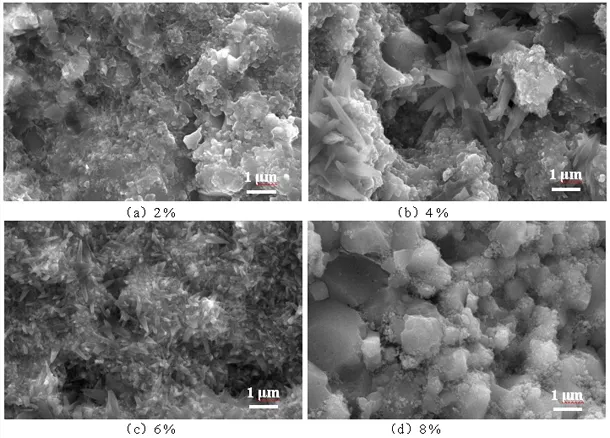
圖17 不同高爐渣添加量的ZTA陶瓷的SEM圖
為了研究不同高爐渣添加量對ZTA陶瓷燒結的影響,進一步分析了ZTA陶瓷的微觀結構,不同高爐渣添加量的復合材料斷面形貌如圖17所示。從圖(a)中可以看出,2%高爐渣的添加不會顯著改變ZTA陶瓷的顯微結構,Al2O3棒狀晶粒的形成幾乎無法顯現。如圖(b)進一步添加高爐渣(4%)可以顯著呈現棒狀生長的Al2O3晶粒,這與其他文獻報道的結果相一致[16-18]。高爐渣在燒結過程中形成微晶玻璃,在Al2O3晶界的偏析,通過增加晶界處Al3+和O2-之間的離子鍵來抑制晶界擴散系數。因此,高爐渣添加量越大,晶粒越細,除ZrO2晶粒尺寸減小外,Al2O3與ZrO2之間的界面也越強。盡管ZrO2和Al2O3晶粒分布均勻,但仍不能避免細小的團聚。進一步添加高爐渣(6%)顯著改變了ZTA陶瓷的微觀結構,足夠多的Al2O3晶粒發生棒狀生長,包裹在團聚體周圍,相互聯鎖,從而降低致密性,因此,在微觀結構中出現更多具有更大尺寸的孔隙如圖(c)所示。隨著高爐渣含量的升高(8%),1 550 ℃燒結并經過析晶處理析出的Ca2Al2SiO7微晶相也相應增多(圖18),ZrO2晶粒在ZTA基體中的團聚程度增加,結合圖(d),此時ZrO2顆粒長大嚴重,超出臨界尺寸,增韌效果較弱,材料內部缺陷增多,所以材料的抗彎強度及斷裂韌性下降嚴重。
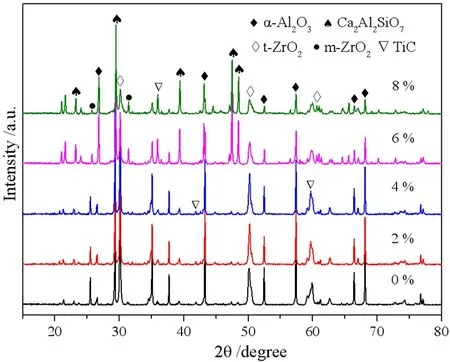
圖18 不同高爐渣添加量的ZTA陶瓷的物相圖譜
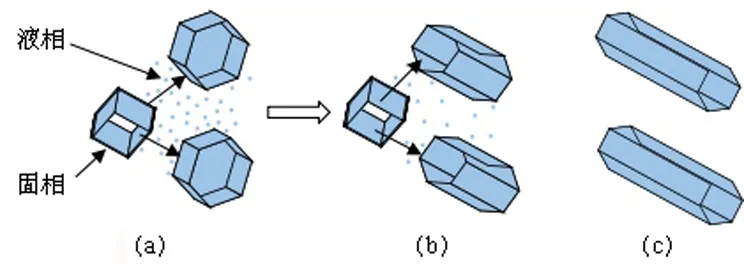
圖19 Al2O3晶粒棒狀生長模型
將高爐渣添加到ZTA陶瓷基體中,隨著燒結溫度升高,晶粒和晶界之間的活性增加,高爐渣在Al2O3晶界之間生成液相,削弱了Al2O3晶粒之間的結合作用,為Al2O3晶粒的自由生長提供了強有力的條件。因此,Al2O3晶粒以各向異性方式自由生長,如果生長動力足夠,就會長成棒狀晶體。
4 結論
(1)添加15%納米α-Al2O3和2%納米TiC,1 650 ℃燒結30 min制備的ZTA陶瓷,相對密度為99.5%,顯氣孔率為0.2%,ZTA陶瓷的抗彎強度和斷裂韌性分別為615 MPa和5.58 MPa·m1/2。
(2)當ZTA復合材料中添加4%的高爐渣,1 550 ℃燒結30 min,低溫下力學性能得到明顯提升,抗彎強度和斷裂韌性分別為650 MPa和6.03 MPa·m1/2,比相同溫度下未添加高爐渣時分別提高了15%和14.2%,燒結溫度降低了50 ℃以上。
(3)高爐渣在燒結過程中,在Al2O3晶粒界面間產生的液相促進Al2O3晶粒的自由生長,驅動力足夠大會生長為棒狀晶,在受力過程中棒晶的拔出和裂紋的偏轉有利于ZTA陶瓷力學性能的提升。